江苏常州明顺电器有限公司
【摘要】 介绍了移动定位衬片的冲压成形工艺分析,载体的合理选择与配置,带料排样方案的确定和比较,级进模模具的总装结构设计。
1 冲压件的工艺性分析
图1为冲压件的零件图,材料为10钢板,料厚δ=1mm。图2为冲压件展开图形。
冲压件的冲压基本工序由外形冲切、冲2-ϕ2.6mm和2-ϕ2.8mm圆孔、3处向上90°直角弯曲成形、2处冲长条凸筋、2处压印冲小圆凸台、2处Z形成形组成。冲压件的主要尺寸精度要求为2-ϕ2.8mm圆孔的孔位间定距尺寸。
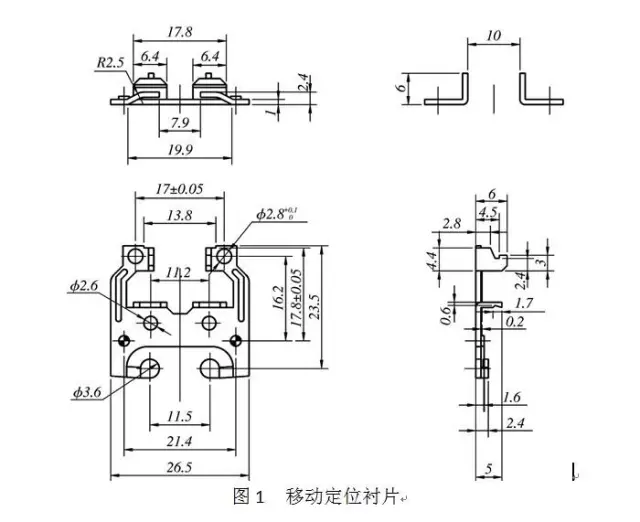
为适应批次生产要求,保证稳定、一致的冲压件质量,采用级进模冲压加工是最佳的生产方式。
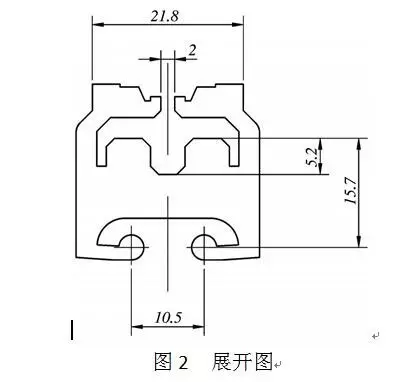
该制件的压筋、冲凸台、Z形成形、3处垂直弯曲的成形方向均同为向上成形,如图3所示。由于冲压件的冲压面积较小在选择冲压工序方案时,有的成形工序可放在同一工位次上进行,而有的成形工序间的位置尺寸距离较小应分解在不同工位上进行,以避免影响到模 具的工作强度及可能产生的模具工作零件间设置时形成的相互干涉。

级进模冲压、冲裁首先要把弯曲部分的局部外形先冲切出来,以留出足够的成形空间。因此,在排样设计时既要考虑冲裁排列顺序的合理性又要保证制件分工位冲切后的外形质量。既要确保带料在连续送进的冲压过程中与冲压件的连接强度又要保证凹模各型孔间应有的工作强度。
综合以上因素,在分析制件展开图形后,针对该冲压件有多处弯曲、成形的特点,并结合级进模带料在连续送进冲压过程中的连接强度。初步确定冲压件材料采用旋转90°单列直排并配置双侧载体的排样方案,如图4所示。由于冲压件有多处弯曲、成形需在相邻的不同工位上连续冲压成形,为保证冲压件质量的一致性,在模具结构设计时应充分注意采用相关工艺措施来达到这一要求。考虑到2-ϕ2.8mm圆孔有相对位置尺寸的精度要求,该2圆孔放在最后冲裁工位上进行(第6工位)。
2 级进模带料排样图设计
因冲压件的材料面积较小,多处弯曲、成形部位的位置距离尺寸亦相对较小。因此,在局部外形冲切后,首先把两端部的压印、2个小圆凸台放在同一工位上成形。在随后的工位上冲压出左、右两条凸筋。在剩余的局部外形冲切后,再在后续工位部位上进行Z形成形及3处向上90°垂直弯曲。2-ϕ2.8mm圆孔放在最后载体与冲压件分离冲切工位上进行。
①冲2个借用导正钉孔 ②局部外形冲切 ③冲2个小圆凸台、两端部压印 ④压左、右2条凸筋、局部外形冲切 ⑤2处向上Z形成形、3处向上垂直弯曲成形 ⑥冲2个定位圆孔 ⑦空工位 ⑧冲压件与载体冲切分离
带料在模具中的定位采用了以冲压设备附设的送料器为粗定位、模具内设置的导正钉为精定位。为不使带料的材料利用率降低太多,同时保证各工位间的定距精度,确定排样设计方案时,借用了冲压件上原有的2-ϕ2.6mm圆孔作为双排导正钉的孔结构 形式。
在工序排列时应先把需弯曲成形的各局部外形部位先冲切出来,同时考虑到级进模在冲压过程中带料必须浮离凹模平面一定的高度,在局部外形的切割工序分解中应将切割长度尽可能减小,以保证带料与制件的连接强度和带料在冲压过程中的平稳送进。因此,把需弯曲的局部外形切割分解成2个冲切工序分别设置在2个不同的工位上,排样设计采用了双侧载体的结构形式。
根据冲压件与双侧载体的连接形式,在最后工位,冲压件与载体的冲切分离只能利用其局部外形形状平切的切割方式。经计算分析,各工序顺序排列后,凹模等模具工作零件的工作强度足够,只在最后冲压件与载体切割分离的前一工位设置了一空工位(第7工位)。
排样方案中带料所占的冲压面积适中,因而模具的面积亦不大。除冲压件自身结构形成的工艺废料外,冲裁形成的工序废料不多,故材料利用率为47.8%。确定的排样图其工位顺序排列如下:①冲2个借用导正钉孔:②局部外形冲切:③冲2个小圆凸台、两端端部压印:④压左、右两条凸筋、局部外形冲切:⑤3处向上90°垂直弯曲成形、2处Z形成形:⑥冲 2-ϕ2.8mm定位圆孔:⑦空工位;⑧冲压件外形与载体平切分离。带料宽度为31mm,各工位间距尺寸为28.5mm,导正钉孔为借用冲压件上的2~ϕ2.6mm圆孔。
级进模工位间距精度对冲压件的质量有直接的影响,如工位间距存在误差,不仅影响冲压件的外形尺寸,还会影响冲压件的内、外形相对位置精度。而影响级进模工位间距精度的主要因素有:①制件的精度等级:②制件所用的材料:③制件内、外形的复杂程度:④模具的总工位数:⑤条料的送进与导向方式:⑥带料在模具内送进的定距形式等。因级进模工位间距精度的计算方法已有多种资料介绍,这里不再细述。该排样工位间距精度经计算并结合模具工作制件加工设备精度的实际情况,精度误差确定为±0.01mm。
3 模具结构与总装设计
模具的总装结构如图5所示。
导正钉头部应设计成抛物线形状,以保证导正钉对带料上导正钉孔的导入。导正钉一般按冲压件的不同冲压加工要求固定在凸模固定板内或卸料板内。未冲压前其工作圆直径部分应高出卸料板平面1.5倍的料厚。要特别注意的是,在模具工作行程较大时(≥15mm以上时),导正钉应设置在卸料板内,否则会形成导正钉在带料的导正钉孔内来回移动的距离过大而加速导正钉的磨损,本级进模的精定距导正钉34设置在卸料板21内。

1.卸料定距套管 2、12、44.内六角螺钉 3.载体分离冲切凸模 4.冲2圆孔凸模 5、22、24.圆柱销 6.模柄 7、10、11.局部外形冲切凸模 8.压印凸模 9.卸料弹顶杆 13.冲导正钉孔凸模 14.卸料板内导套 15.导柱 16.上模座 17.上垫板 18.凸模固定板 19.卸料板内成形镶块 20.卸料板垫板 21.卸料板 23.凹模内Z形成形镶块 25.卸料板内弯曲镶块 26.凹模板内导套 27、33、38.螺塞 28.矩形截面弹簧 29.成形弹顶块 30.凹模内上弯曲凸模 31.带槽浮顶导料柱 32、37.圆形截面弹簧 34.导正钉 35.凹模内压圆凸台凸模 36.凹模内压凸筋凸模 39.成形弹顶块 40.凹模内上弯曲凸模 41.凹模 42.下垫板 43.下模座
级进模(除纯冲裁级进模外)大多为立体冲压的工序组合。因此,带料在送进过程中必须浮离凹模平面一定的高度。带槽浮顶导料柱兼具导料与浮顶两大功能,结构简单,导料柱之间的空间较大,与模具中的其他工作制件和结构件间产生干涉的可能性亦较少,有利于垃圾的清除与故障的排除。因而本级进模使用了该结构形式的导料装置(件31、外径为ϕ6mm)。
其与凹模孔的配制间隙为H7/f6。同时,为使带料平稳浮离凹模平面,在各浮顶导料柱后部的弹顶力必须一致,带槽浮顶导料柱的热处理硬度一般为50~55HRC。在最后工位,冲压件与载体冲切分离后由压缩空气吹离模具,而载体作为废料被全部切入凹模后排出。
卸料板采用了经热处理的弹压卸料板结构形式。因冲压件全部向上的压凸、压筋、Z形成形、垂直弯曲成形的模具零件(分别为件23、35、36、40)均为向卸料板21内成形。故在模具结构设计时,卸料板与一般外形简单的凸模配合方间隙为0.01~0.02mm,与复杂外形凸模的配合间隙为0.02~0.03mm。因本级进模的卸料力适中(一般需进行校核),故经计算后采用了矩形截面中载荷弹簧28。为保持卸料力的平衡,卸料弹簧应对称、均衡设置。同时为保证弹压卸料板对凸模的导向精度和对各凸模特别是小凸模的保护,在上模部分设置了辅助导柱15,数量为4个,在卸料板内设置导套,凹模内也设置了导套26,冲压中该辅助导柱同时亦可抵消一部分弯曲成形时产生的侧向力。
全部圆形凸模及异形凸模均采用与凸模固定板台肩固定连接的结构形式。最后载体冲切的凸模设计成把所有载体完全切入凹模的结构形式,以使冲压件(留在凹模平面由压缩空气吹离模具作业区)与废料(载体从凹模下排出)完全分离。
模具的模架选用了钢结构的对角滚珠导柱导向模架。以适应高速、连续的冲压加工需要。除异形工作零件、卸料零件、定位零件外,其它零件选用了模具专业厂家生产的标准件,如导柱、导套、标准模板、矩形截面弹簧、圆形凸模等等。一般截面的异形凸模用专业厂家生产的圆形凸模改制也比较方便。可以降低模具成本和缩短模具的制造周期。

|